Precision Chillers for Pharma & Chemical Industries
High-performance chillers for pharmaceutical manufacturing, chemical processing, and soap production. Ensure temperature control, safety, and product quality.
Why Chillers Are Essential in Pharma & Chemical Sectors
Temperature control is critical in pharma and chemical processes to:
- Maintain product consistency and stability.
- Prevent overheating in exothermic reactions.
- Ensure compliance with safety and quality standards.


Chillers in Soap Production
1. Soap Plodder Cooling
Process: A plodder kneads and extrudes soap into bars, generating heat that softens the mixture.
Chiller Role: Maintains soap temperature at 60–70°F (15–21°C) using glycol or water-cooled systems.
Prevents stickiness and air pockets for smooth, uniform bars.
Equipment: Cooling jackets or heat exchangers integrated into the plodder.
2. Soap Stamping/Printing Machines
Process: Stamping molds soap into branded shapes; improper cooling causes deformation or sticking.
Chiller Role: Circulates -30°C to -15°C glycol through stamping dies to solidify soap instantly.
Ensures crisp designs and easy mold release.
Equipment: Low-temperature glycol chillers with cooling plates.
Key Chemical & Pharma Applications
Pharmaceutical Manufacturing
- Reactor Cooling: Controls exothermic reactions during drug synthesis.
- Lyophilization (Freeze Drying): Condenses solvents in freeze-drying systems.
- Crystallization: Manages crystal formation for APIs (active pharmaceutical ingredients).
Petrochemical Industry
- Distillation Units: Cools condensers in crude oil refining.
- Polymerization Reactors: Prevents runaway reactions in plastic production.
Fine Chemicals & Cosmetics
- Emulsification Tanks: Maintains stable temperatures for lotions and creams.
- Mixing Systems: Prevents ingredient degradation in high-shear blenders.
Semiconductor Manufacturing
- Etching/Deposition Chambers: Ensures precision in microchip production.
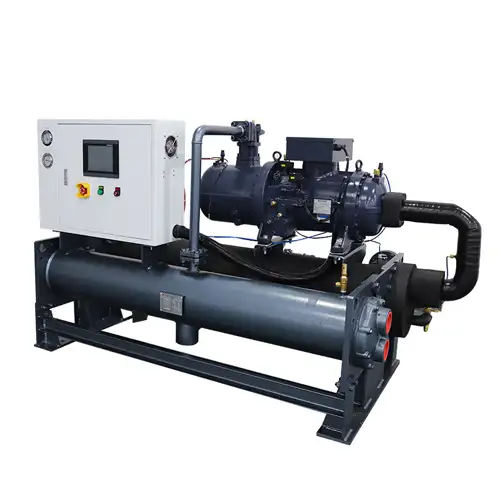
Benefits of Our Chillers
✔️ Industry-Specific Designs: Corrosion-resistant materials (titanium, stainless steel) for harsh chemicals.
✔️ Precision Control: ±0.5°C accuracy with PLC automation.
✔️ Energy Efficiency: Variable-speed compressors reduce energy use by 25%.
✔️ Scalability: Modular systems for small labs to large plants.
Why Choose Us?
- 20+ Years Expertise: Custom solutions for pharma, soap, and chemical sectors.
- 24/7 Support: Rapid response to minimize downtime.
- Certified Compliance: Meets FDA, GMP, and ISO standards.